AUTOMOTIVE CABLES
01
FEASIBILITY
It all starts with an Idea
The design process starts with a comprehensive feasibility study: this study provides us with a detailed assessment of the existing conditions and needs, making it possible to deliver high-quality solutions within the agreed time and budget.
Our young and structured technical office performs a preliminary examination to determine the technical and functional specifications of each solution.
If necessary, our expert technicians can also provide valuable co-design support.
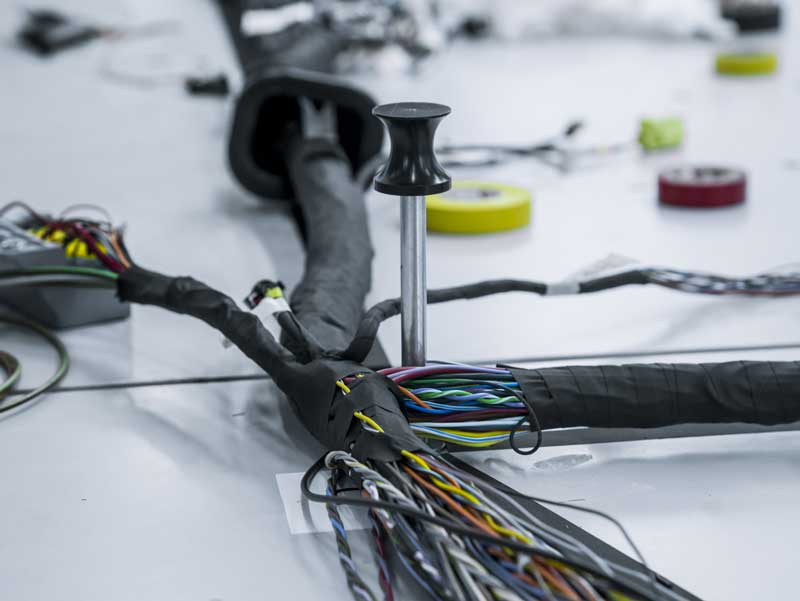
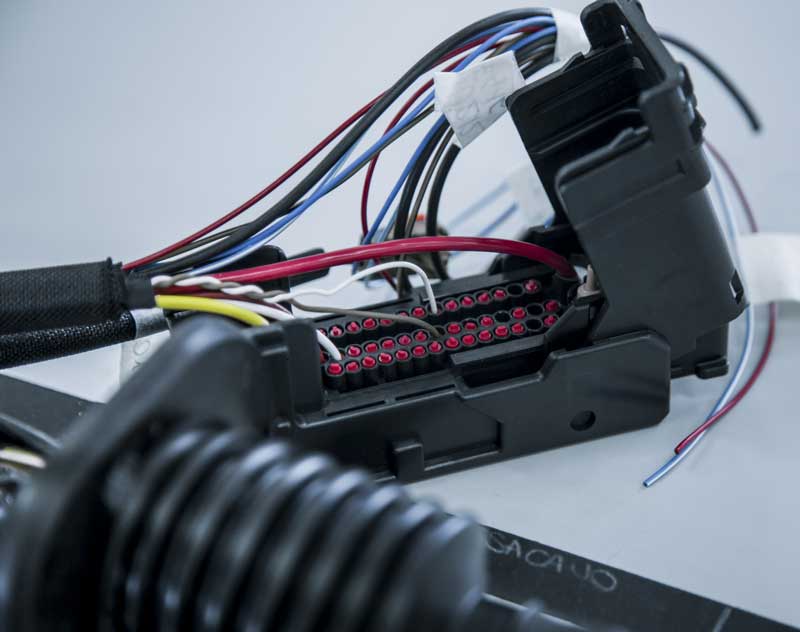
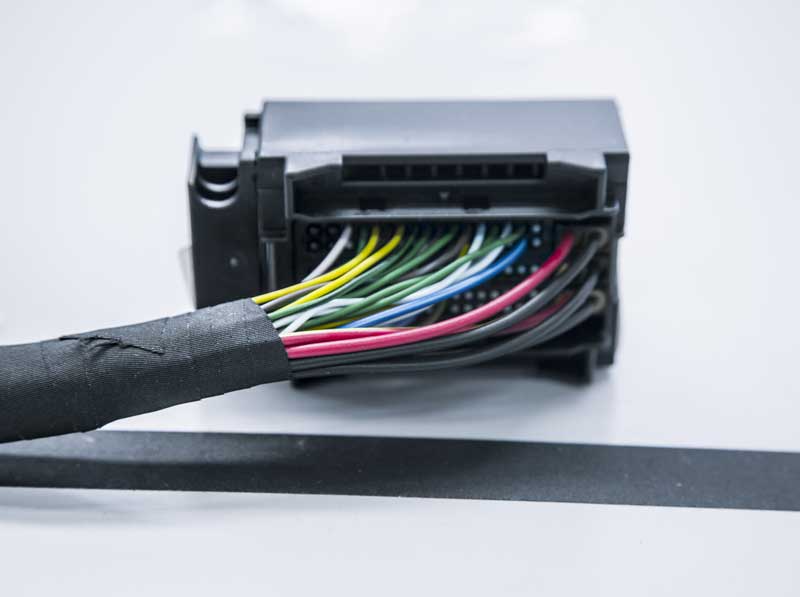
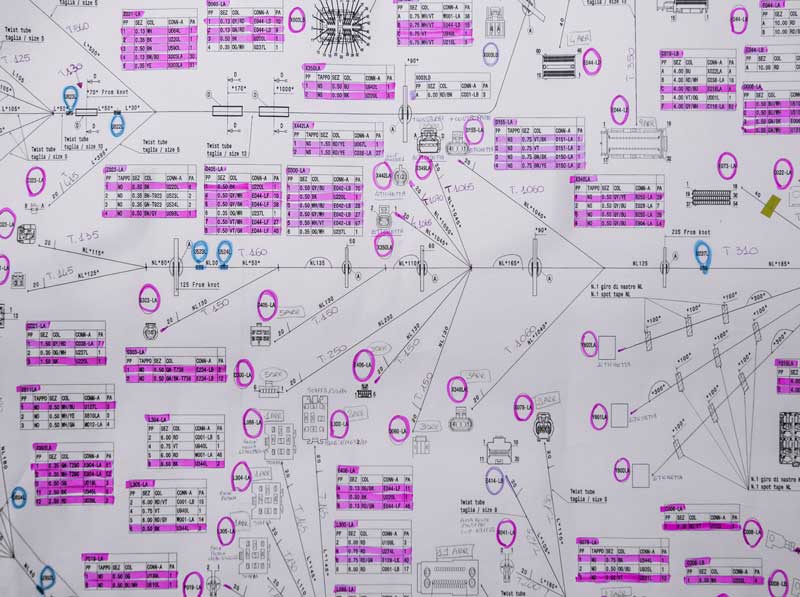
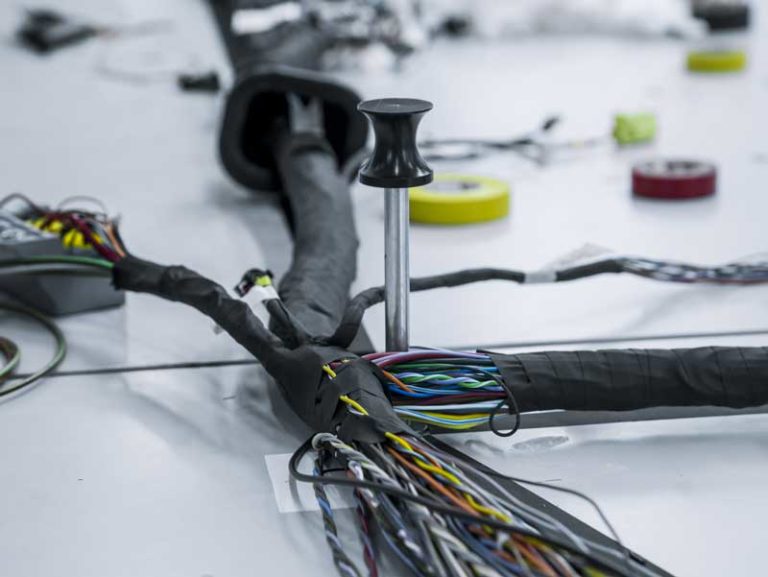
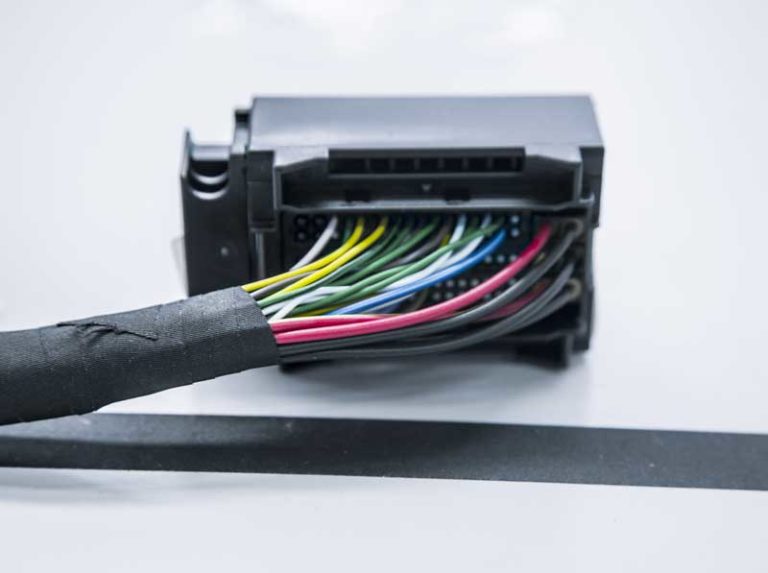
02
PROTOTYPING
A perfect synthesis of science and technology
The feasibility study is a crucial stage of our process: it has a variable duration ranging from 6 to 12 months.
This test is particularly important, especially in case of complex processing, as it helps us highlight potential weaknesses as well as areas for improvement.
Once the specifications accurately match with industry standards and regulatory requirements, the result is to be considered as the starting point of the manufacturing process.
03
ASSEMBLY
Balance is the key to success

TECHNOLOGY
Once the design and prototyping processes has been successfully completed, the assembly phase begins. The manufacturing process is carried out thanks to modern, cutting-edge machinery that ensure high accuracy, repeatability and time optimisation.

WELDING
Welding is performed using ultrasonic technology: a method that makes it possible to join two or more cables (up to 35mm) without the addition of filler materials. A sophisticated touch screen interface allows operators to monitor all critical and technical parameters throughout the process.

CUTTING
We have an internal division dedicated solely to the cutting of cables. This procedure is fully automated: crimp tooling with force control applied.

SHEATH
To ensure that the joints are weather resistant, a protective sheath is applied with Raychem-ILS equipment. To ensure that the joints are weather resistant, a protective sheath is applied with Raychem-ILS equipment.
03
ASSEMBLY
Balance is the key to success

TECHNOLOGY
Once the design and prototyping processes has been successfully completed, the assembly phase begins. The manufacturing process is carried out thanks to modern, cutting-edge machinery that ensure high accuracy, repeatability and time optimisation.

WELDING
Welding is performed using ultrasonic technology: a method that makes it possible to join two or more cables (up to 35mm) without the addition of filler materials. A sophisticated touch screen interface allows operators to monitor all critical and technical parameters throughout the process.

CUTTING
We have an internal division dedicated solely to the cutting of cables. This procedure is fully automated: crimp tooling with force control applied.

SHEATH
To ensure that the joints are weather resistant, a protective sheath is applied with Raychem-ILS equipment. The sheath allows to monitor and control the temperature and duration parameters of the thermo-retraction cycle.
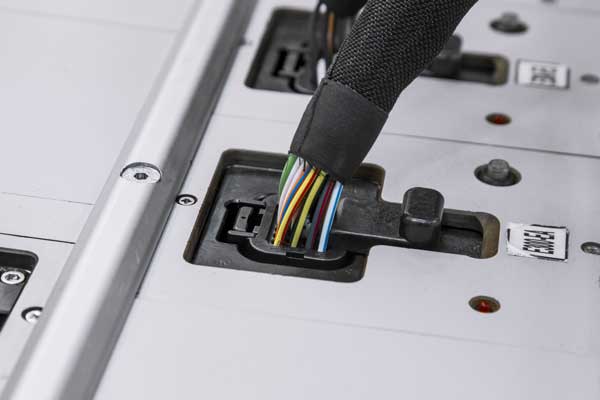
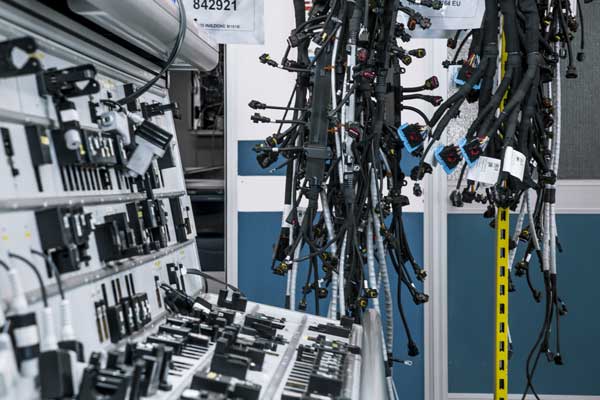
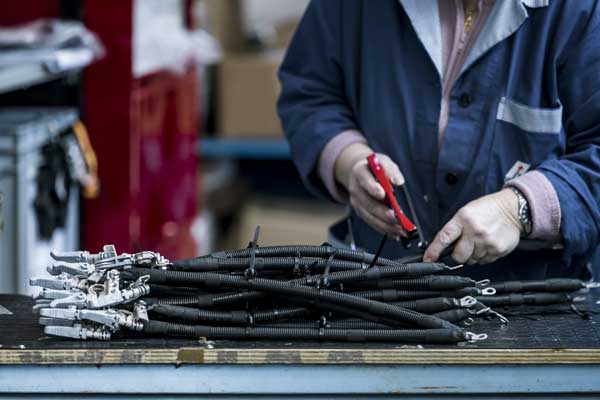
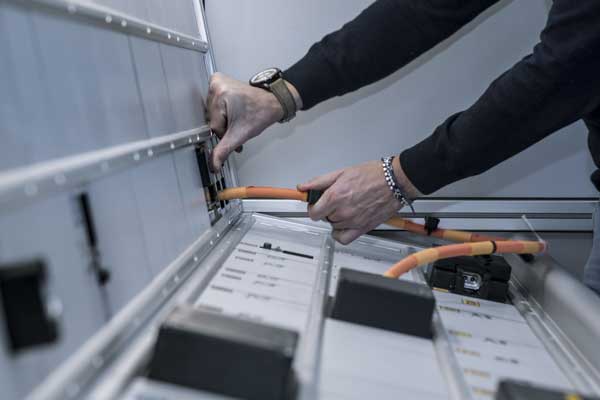
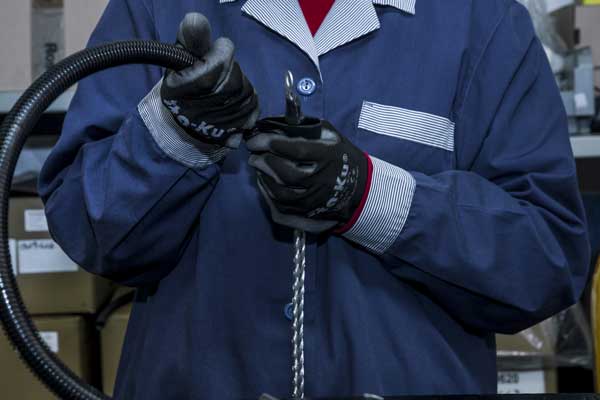
04
TESTING
Excellent result, total safety
Final tests are performed on all cables through both visual and automated test benches.
This versatile control method can be adjusted depending on the product type.
The test ends with the realease and application of an adhesive label which – upon request – can be customised with:
- Barcode
- Production batch
- Operator identification code
- Date of the test
04
TESTING
Excellent result, total safety
Final tests are performed on all cables through both visual and electronic test bench.
This versatile control method can be adjusted depending on the product type.
The test ends with the realease and application of an adhesive label which – upon request – can be customised with:
- Barcode
- Production batch
- Operator identification code
- Date of the test
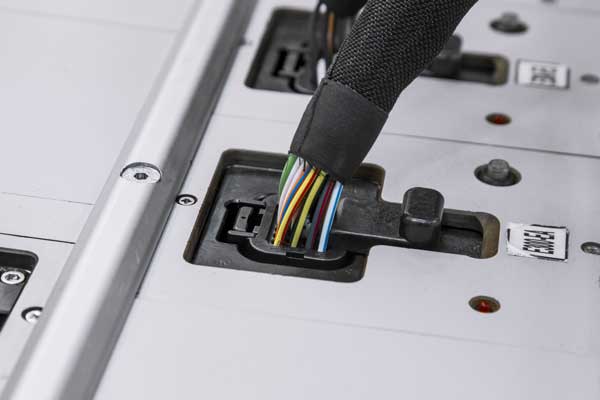
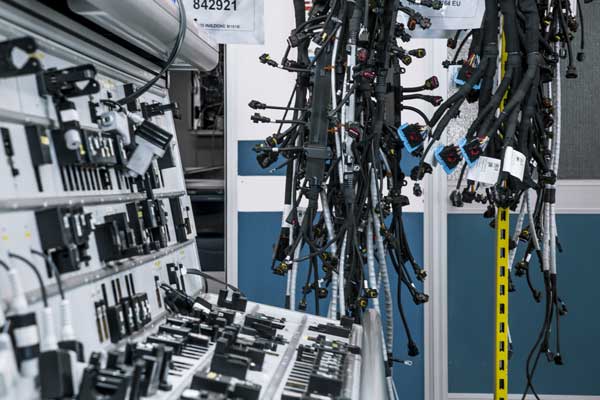
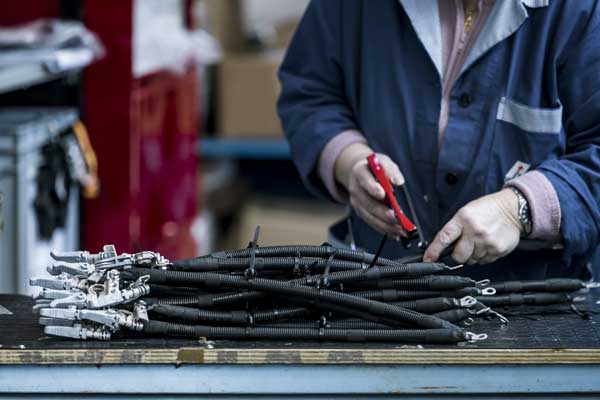
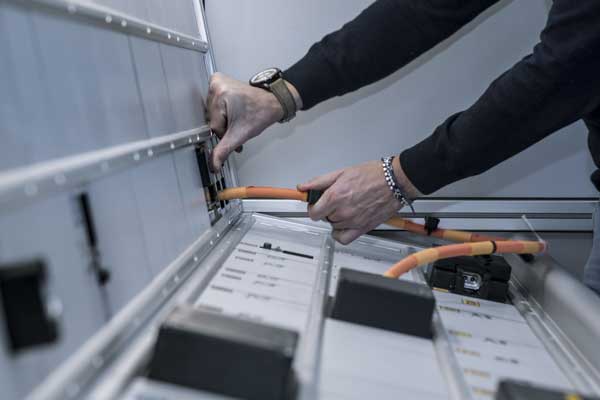
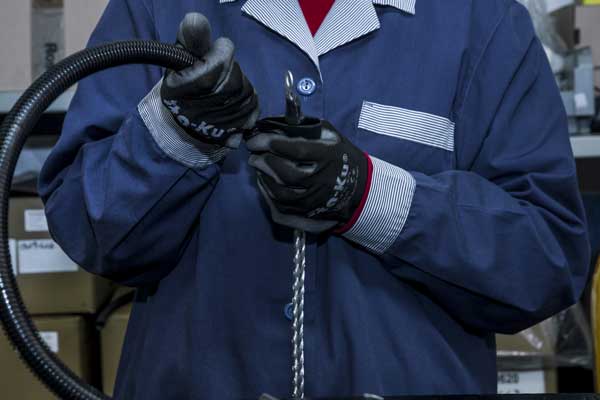